How to Deploy A.I. Solutions in Welding – From Pilot to Factory Floor in a Month
- Rafal Maciag
- Dec 9, 2024
- 3 min read
Welding, a craft traditionally reliant on human expertise, is being revolutionized by Artificial Intelligence. A.I. solutions now offer precision, automation, and adaptability, enabling factories to achieve Industry 4.0 transformation. Here’s how you can deploy an A.I.-powered welding system within a month—delivering tangible results and preparing your team for scalable success.
1. Install the Vision System (1 Day)
The journey starts with installing a welding camera and compute unit integrated with your robotic system. Supporting TIG, MIG/MAG, and plasma processes, this hardware setup takes just one day. Once installed, it captures and processes welding data while seamlessly connecting to your PLC or robotic arm.
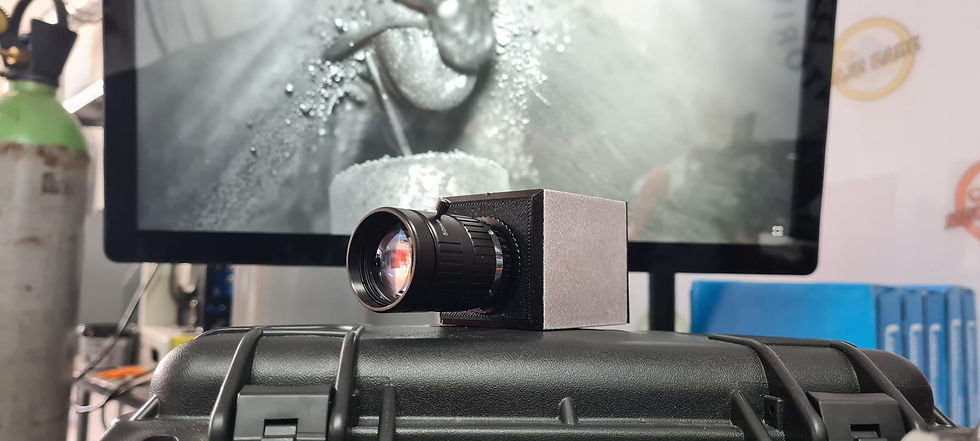
2. Gather initial Data (2-3 Days)
Over the next few days, the system records welding operations, creating datasets tailored to your production needs. These datasets are used to identify and analyze critical elements like gaps, joints, and defects.
Factories often worry about data security, especially when dealing with proprietary technologies or processes. With our platform, all data remains under your control, whether stored on-premises or in the cloud.
3. Train the Model and Augment Control Points (2-3 Days Initially)
This phase transforms raw data into actionable intelligence. Here's how:
Labeling: Operators label key features, such as weld seams or defects, using an intuitive platform interface. With our pre-trained models labeling is much faster. In most of the cases, you only need to fix or slightly adjust the already annotated polygon.
Training: The labeled dataset is used to train the A.I. model. Training can be done in the cloud or on-premise, with training times ranging from a few hours to—rarely—days, depending on the complexity of the model.
Control Point Design: The first iteration includes designing control points that guide the robotic arm. These points are overlaid in the camera’s view and calculated using post-processing techniques. This initial design process typically takes 2–3 days.
Once the first iteration is complete, subsequent refinements can be done in hours. Each cycle sharpens the model’s accuracy and adaptability to specific welding conditions like material deformation or unique geometries.
4. Enable Full Automation (A Few Days)
The final phase integrates the A.I. model with the PLC, enabling dynamic robotic control. The system now guides the robotic arm with precision, adapting in real time to irregular surfaces or other variations. Full automation transforms your welding operation, boosting efficiency and quality.
The Common Factory Story: Robots That Sit Idle
The journey toward Industry 4.0 often begins with a significant investment: a factory’s first robotic arm. This purchase is made with high expectations—automating repetitive tasks, improving quality, and boosting productivity.
But here’s what frequently happens next:
The robot is installed but remains unused.
It lacks programming specific to the factory’s needs.
There’s no one on-site with the expertise to program or adapt the robot.
The excitement quickly turns into frustration. Managers realize that a robot without programming is just an expensive paperweight. Eventually, factories bring in external specialists or spend months training employees to program robots, delaying the return on investment and creating additional costs.
A Smarter Path Forward
This is where our platform makes a difference. Instead of relying on external developers or prolonged learning curves, we empower your automation engineers to:
Train A.I. models specific to your welding processes using labeled datasets.
Deploy A.I.-driven automation quickly, leveraging pre-trained models and fine-tuning them for on-site scenarios.
Gain independence by learning how to manage, adapt, and scale robotic operations.
The result? Your team becomes self-sufficient, transforming robots into productive assets within weeks—not months.
Why This Works
Scalability Built In
Once the pilot system is operational, scaling to additional stations is seamless. Reuse datasets, replicate trained models, and manage the fleet—all from a single platform.
Training Designed for Engineers
Our approach is unique: instead of relying on external developers, we focus on enabling your team. This ensures long-term success and reduces dependency on external resources.
Flexibility for Any Process
Whether it’s detecting defects, welding irregular geometries, or adapting to new materials, our solution is customizable to your needs. Today, AI is so affordable, that it fits solutions with PLC starting from just 200$ and ending with robots worth a couple of hundred thousand dollars.
From Pilot to Factory Floor
In just one month, you can deploy and validate an A.I.-powered welding solution, empowering your factory for Industry 4.0. More importantly, you’ll have a trained team ready to scale the solution across your operations.
Stop letting your robots sit idle—put them to work with the power of A.I.
Comments